Metinvest Results: 25% Increase in Equipment Efficiency
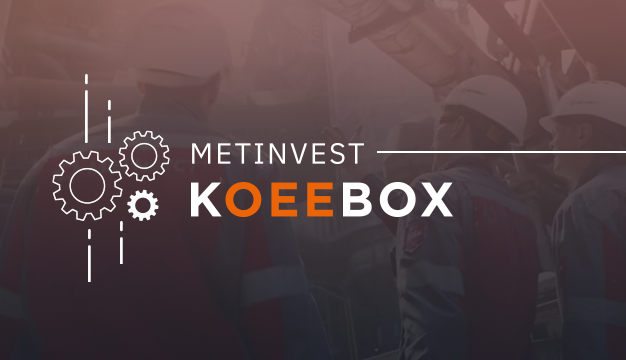
The project, implemented at the Zaporizhia Foundry and Mechanical Plant (hereinafter – ZFMP), became an example of the efficient, simple and economical application of Industry 4.0 technologies. ZFMP is part of the Metinvest Group and fulfills orders for metallurgical production in Zaporizhstal. The project was implemented by the KOEEBOX team with the participation of Metinvest Digital, which implements projects for the digital transformation of production and business units for Metinvest enterprises.
The Main Goals of the Enterprise
Zaporizhzhya Foundry and Mechanical Plant has two important goals:
- Maintaining the speed and quality of order fulfillment. Products are manufactured in full compliance with labor protection requirements and meet the specifications set by the customer.
- Cost reduction to compete on cost.
To achieve the set goals, it is important to control the work of the enterprise at all stages, effectively use the installed equipment, constantly monitor development trends and implement advanced modern technologies. One of the important stages in the transition to smart production is the monitoring of overall equipment efficiency (OEE).
What Is OEE?
Overall Equipment Performance is a way to analyze equipment performance. The OEE calculation helps to answer the questions that arise at each production plant: “How efficiently is the equipment used?”, “What does reduce its efficiency and how to deal with it?” etc. In other words, OEE reflects the real state of affairs in production, helps to improve its performance and increase profits.
Measuring the OEE involves daily continuous recording of indicators of the state of the equipment and continuous monitoring of production processes.
What Challenges Were Facing ZFMP?
According to Oleksiy Tytarenko, project manager of ZFMP LLC, the main difficulties the team faced during the analysis of opportunities for OEE monitoring were as follows:
- The company has a variety of equipment with different principles of operation. Accordingly, an individual approach is required for each unit.
- Not all equipment can connect to the factory network. For some units, the manufacturer has restricted access, and some equipment cannot connect.
After a long study of the solutions presented on the market, they settled on KOEEBOX as the best option. The devices were installed on the equipment, tested, and then with their help employees began to monitor the effectiveness of the equipment and record its downtime and loading.
How Does the KOEEBOX Work?
The device has the form of a box that connects to equipment that is powered by the mains. It shows the efficiency of machines, and their downtime, monitors the smooth operation of critical equipment, warns of anomalies, and allows to return the equipment to normal. The sensor is universal, so it can be used for any machine – it can be easily installed by employees of the company in 10-15 minutes.
All the information recorded by the device is immediately transferred to a special web application that can be opened at any time on a computer, tablet, or smartphone. Only authorized employees of the enterprise have access to it.
How Does KOEEBOX Help in the Production of ZFMP?
When installing KOEEBOX devices in the production of ZFMP, the target performance indicators of each machine were set. If they cannot be reached – at the end of the shift the system sends a letter to the responsible employees, and they sort out the reasons. If the equipment is idle for longer than the allowable time (e.g. 30 minutes), the system promptly sends a message so that workers can begin to rectify the situation as soon as possible.
Since the company works in two shifts, it is possible to compare the efficiency of the equipment on them. The information obtained from KOEEBOX helps to find the causes of inefficient work and make informed management decisions that can increase production efficiency.
Example of Increasing the Efficiency of the Machine From 12% to 75%
The result of the application of KOEEBOX can be seen in a specific example from the ZFMP. After the modernization of the №164 horizontal boring machine (model 2В622), it was necessary to understand how effectively it is used. Previously, this information was obtained only from the operational reports of the performers, but it may not be objective. The installed KOEEBOX sensor provided unbiased data that allowed to understand in which modes and how exactly the machine is used. It turned out that the real efficiency of the equipment, taking into account the total spent fund is 12-15%.
After the analysis, the specialists of the enterprise determined the criteria by which the reasons for downtime were divided and took measures to improve the efficiency of providing tools, preparing technological programs, and familiarizing personnel with the production culture. All this made it possible to reach the level of the machine efficiency indicator of 75%. In the future, the task remains to keep it and continue to increase.
What Results Have Been Achieved with KOEEBOX?
According to Oleksiy Tytarenko, in addition to the above results, the devices also allow seeing the actual operating time of the equipment – engine hours for each machine. With their help, it was possible to detect a phase shift on one of the machines, which made it possible to warn and prevent its failure. Such information is useful for the engineering management of the enterprise, as its departments can carry out the necessary repairs in advance.
After the management decisions of the company began to be based on reliable and up-to-date information, the team increased the efficiency of connected equipment by an average of 25%, and in some cases by 40%.
Watch the video with this case:

Find out how KOEEBOX devices can change the efficiency of your production – leave a request at https://koeebox.com/ and get a month of free testing of the control system for your equipment.